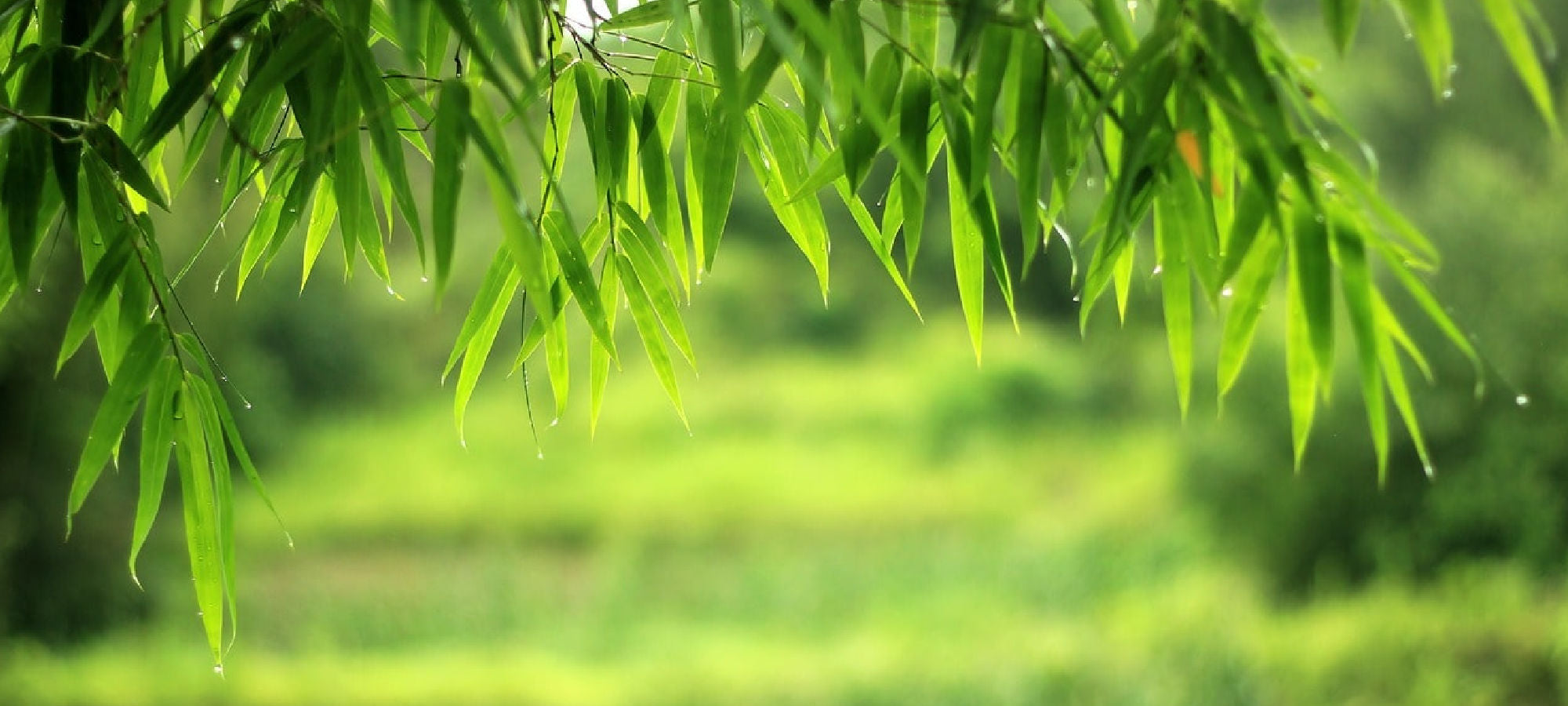
ORIGINS OF OUR BAMBOO SOCKS
YES, WE CAN! JAMES WILL TELL YOU HOW....
James, the co-founder of Swole Panda, has researched and visited each tier of the process, right back to the source of the bamboo. Most brands don’t go past the fabric production stage. We will go beyond. We want our impact positive journey to affect our entire supply chain.
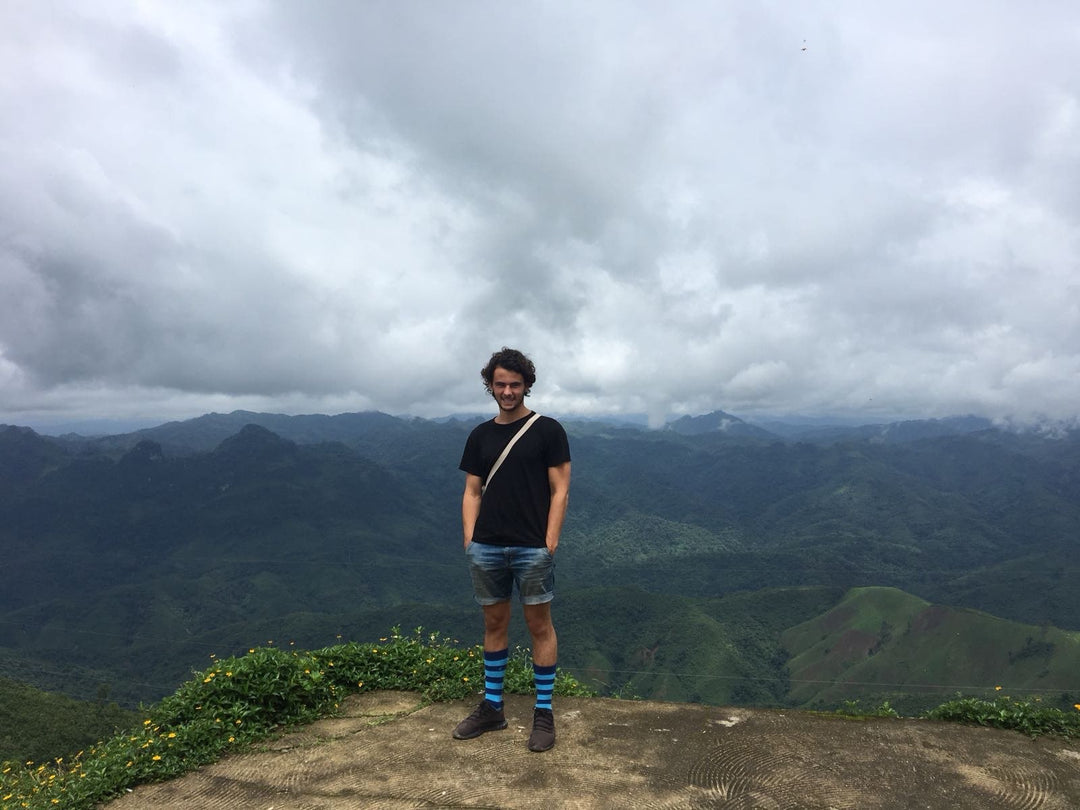
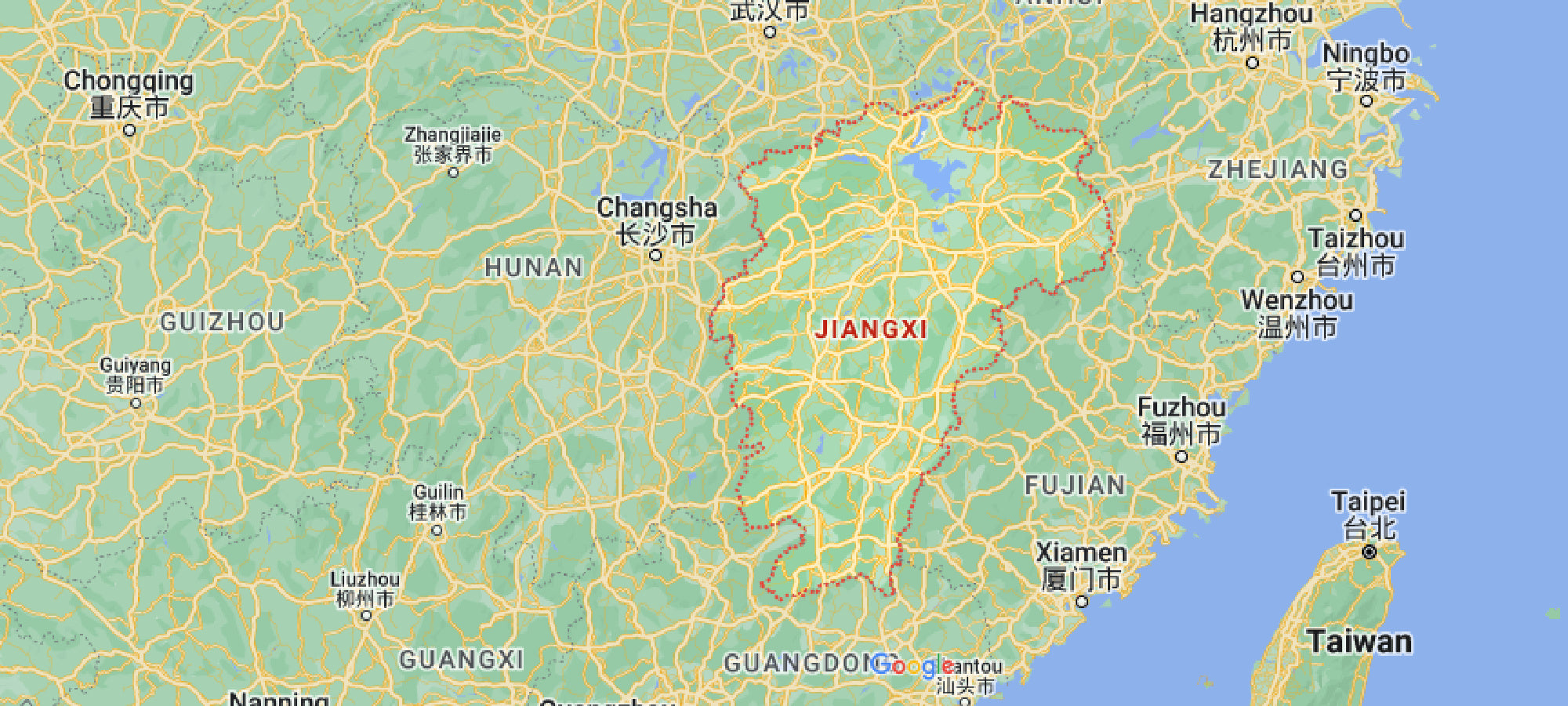
James started with a visit to one of the sustainably managed bamboo forests in China’s Jiangxi Province. The naturally occurring forests contain steep slopes which bamboo can comfortably grow on, maximising an otherwise unusable area.
It grows naturally and super-fast, with yields of up to 10 x higher than cotton for the same area without the need for pesticides.
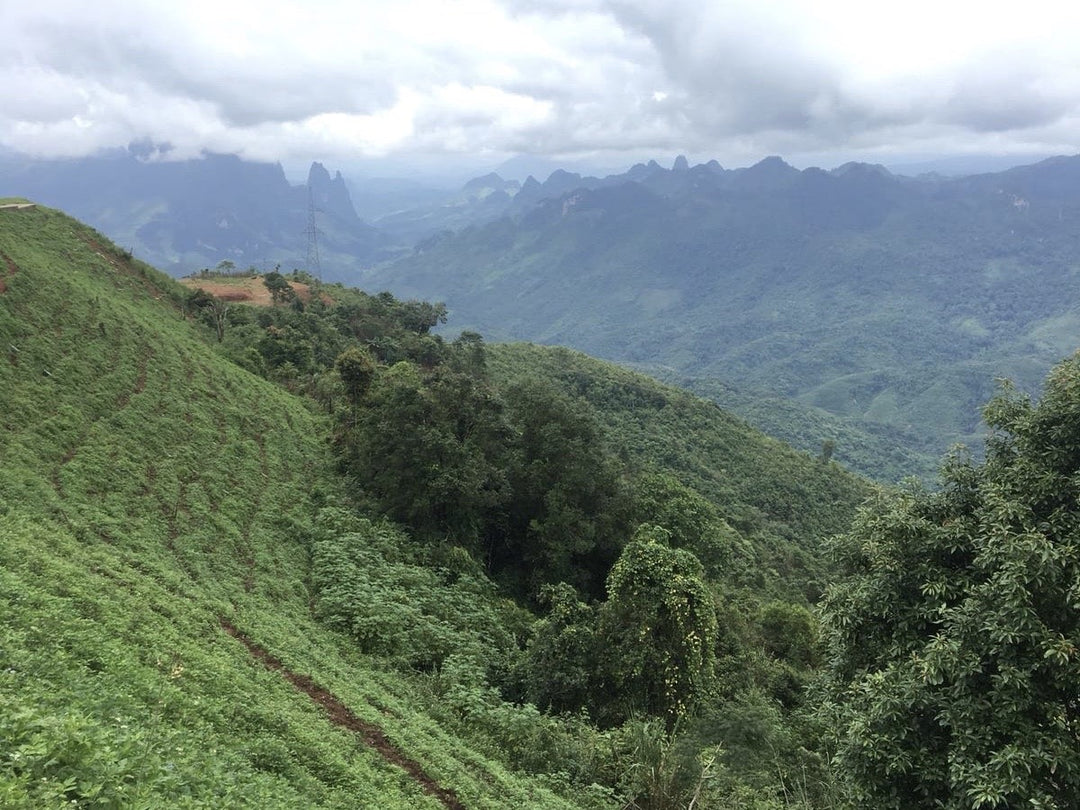
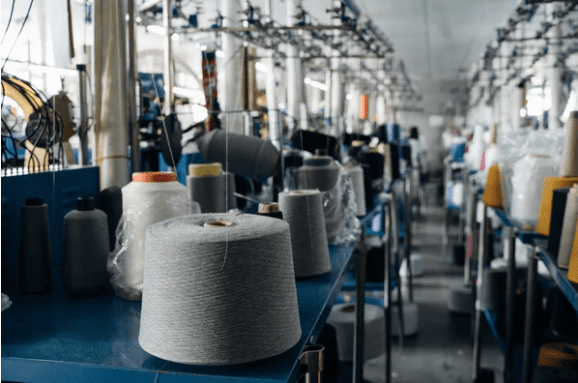
The next step is turning the harvested bamboo into dried pulp which will then be sold onto the fibre producers. Very little is understood in the wider clothing industry about the processes involved this deep into the supply chain.
The factory James visited shares our environmental values, having invested heavily in waste-treatment technology. We now have the knowledge and transparency we need to make our impact positive ambition both possible and really meaningful.
Our biggest concern has always been the rumours about the management of the chemicals required to make bamboo pulp into bamboo lyocell and viscose fibre. We knew we had to find out the truth for ourselves.
As we’d hoped, we found that our producers were taking their environmental responsibility seriously and working within safe limits. Beyond our expectations, one had not only invested millions of dollars in waste-treatment but was committed to becoming a world-leader in sustainable bamboo viscose and lyocell production.
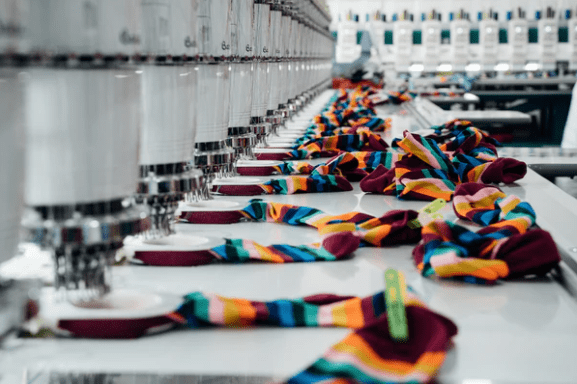
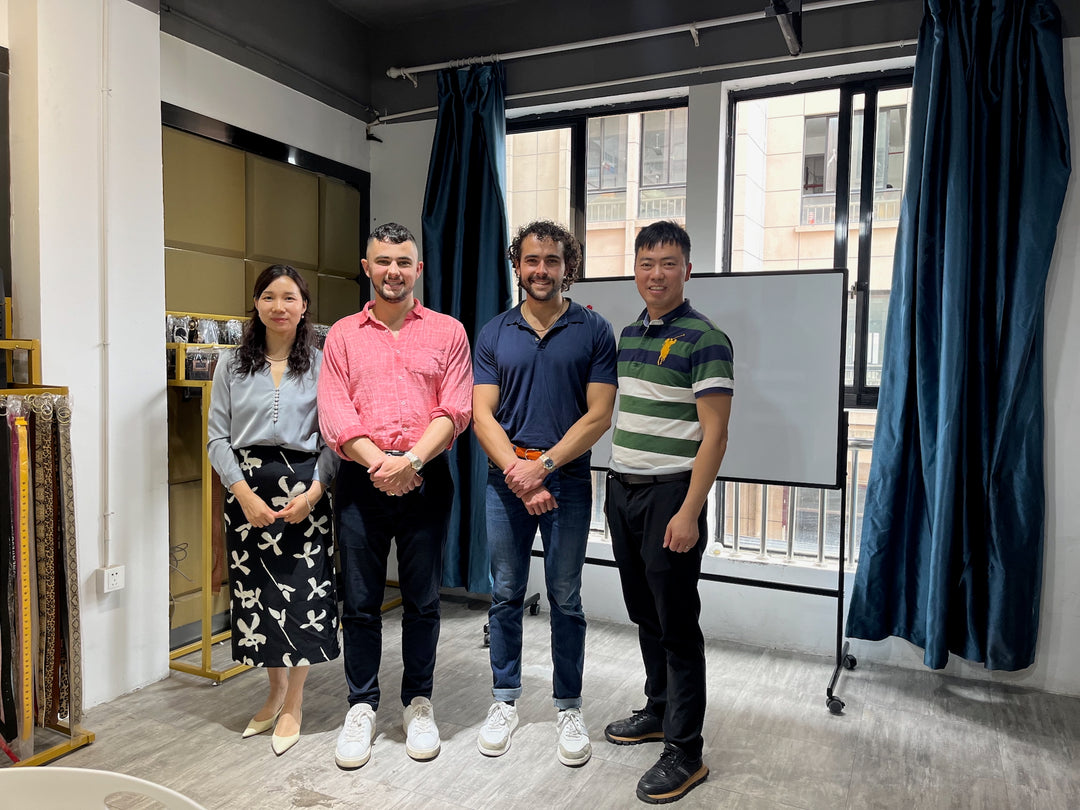
Once the fibres have been knitted into fabric they're transported to our garment factory. We’ve purposefully chosen to work with suppliers who share our values about treating people and the planet respectfully. We try to keep our supply base small and make the effort to build strong relationships and long-term partnerships with them.
We speak to them daily and visit in person as regularly as possible. We believe the best way to know what’s going on in your supply chain is to see it for yourself.